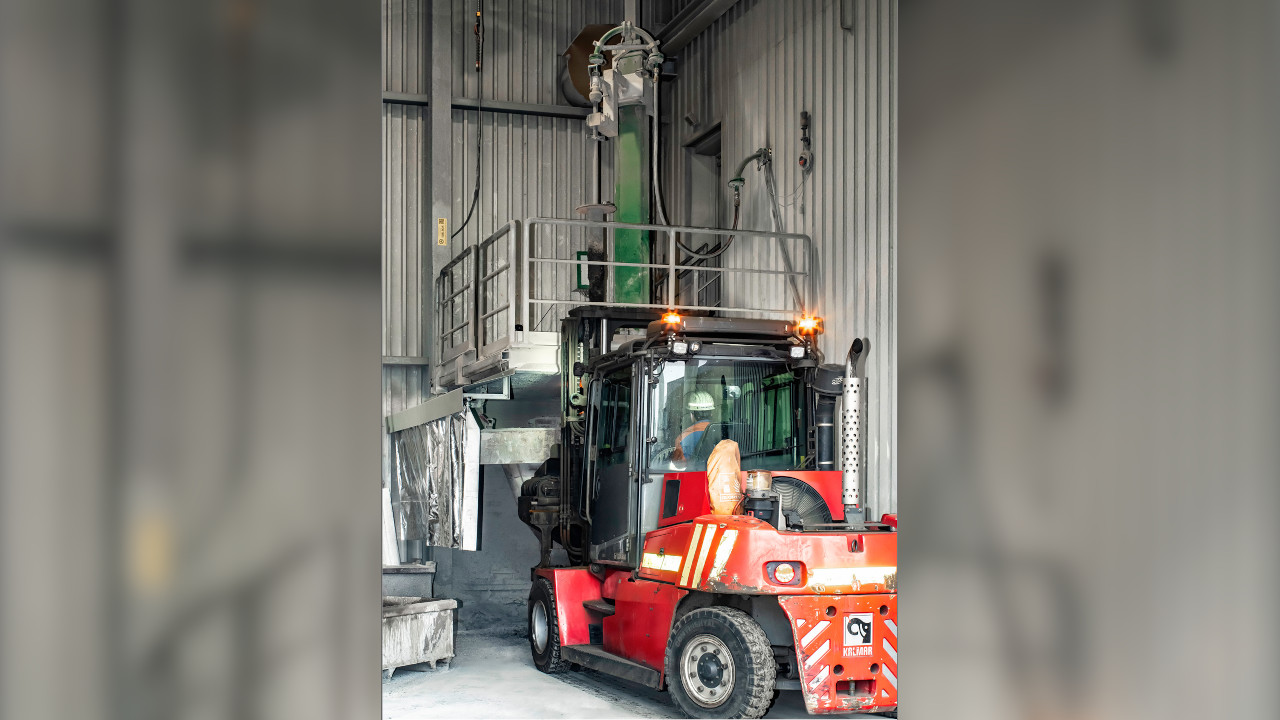
Reducing Global Dependence on Raw Materials
Domestic Lime Instead of Magnesium from Overseas
- von Birte Vierjahn
- 14.05.2024
With 87 percent of global production, China has a near monopoly on magnesium*, an essential raw material for metallurgy. Engineers at the UDE and industrial partners have now developed a process that allows molten iron to be desulphurized to produce spheroidal graphite cast iron without using magnesium. Their results are published in the Journal of Sustainable Metallurgy; a corresponding plant has already been put into operation.
The supply bottlenecks during and after the peak of the coronavirus pandemic have shown the extent to which global dependencies determine our economy. Political demands and considerations in the EU are, therefore, increasingly focused on making Europe's supply of raw materials more independent again.
The Institute for Technologies of Metals (ITM) at the University of Duisburg-Essen (UDE), together with Fritz Winter Eisengießerei GmbH & Co. KG (FW) in Stadtallendorf and the FEhS – Building Materials Institute e.V. in Duisburg has developed a new type of process that uses local lime instead of magnesium for desulphurization. "Something similar is already taking place in the steel industry," explains Prof Dr. Rüdiger Deike, head of the Metallurgy and Forming Technology working group, "but they don't use lime-carbon mixtures like the process we have developed. One of the differences between hot metal from blast furnaces and cast iron are the higher contents of alloying elements like silicon and sulfur etc. in cast iron. In addition, the quantities to be treated per batch in the foundry industry are much lower at 2 tonnes than in the steel industry at 150 to 350 tonnes."
According to calculations (based on 2021), approx. 2,000 tonnes of magnesium could be replaced annually in Germany. That not only reduces the foundry industry's dependence on global raw material markets – the process offers further advantages: After being used for desulphurization, magnesium is finely distributed in a mixture as an oxide or sulfide in the slag, can no longer be economically recycled and is therefore irretrievably lost. On the other hand, Lime-based desulphurization agents are significantly more environmentally friendly, cheaper, and have a lower CO2 footprint – the production process of the raw materials contributes considerably to this. Emissions generated during transport are also significantly lower with the lime-based alternative available domestically.
The fact that the process works in principle was demonstrated on a laboratory and pilot plant scale by ITM in cooperation with FW and OCC GmbH. FW, one of the largest foundries in the world, subsequently developed an industrial-scale system and put it into operation in parallel with normal production, thus proving that the technology can be used on a large scale.
The technology was developed as part of the SUBMAG (2012) and EKALGU (2017) research projects, which were funded by the German Federal Ministry of Education and Research (BMBF).
* source: statista.com, latest information for 2021
Original Publication: https://doi.org/10.1007/s40831-024-00829-y
Image: Plant for injecting powdered lime into a cast iron melt.
Further Information:
Prof. Dr. Rüdiger Deike, Metallurgy and Metal Forming, +49 203/37 9-3455, ruediger.deike@uni-due.de
Editor: Birte Vierjahn, +49 203/37 9-2427, birte.vierjahn@uni-due.de