DFG projects
Elodie Donval, Matti Schneider Modeling binder-jet 3D-printed sand microstructures
The 3D printing of sand cores for casting allows for the design of more complex parts than the usual core shooting process. However, the composite material obtained by 3D printing features thermo-poro-mechanical properties that differ from those of materials produced by conventional methods. In particular, the layer-by-layer sand deposition process results in an anisotropy of the macroscopic properties. The present project, in collaboration with the Fraunhofer Institutes ITWM and IGCV and the University of Augsburg, aims to gain a deeper understanding of the 3D printing process of sand cores. This will enable us to identify the influence of process variables on the end product. To this end, we develop a microstructure generation approach that accurately reproduces the layer-by-layer deposition process of the sand and the addition of the binder. Based on the microstructures created, we evaluate the mechanical, thermal and flow properties and compare them to experimental results. By better understanding the microscopic processes involved in the 3D printing of sand cores, we aim to provide a basis for further development of environmentally friendly materials and optimization of the printing process.
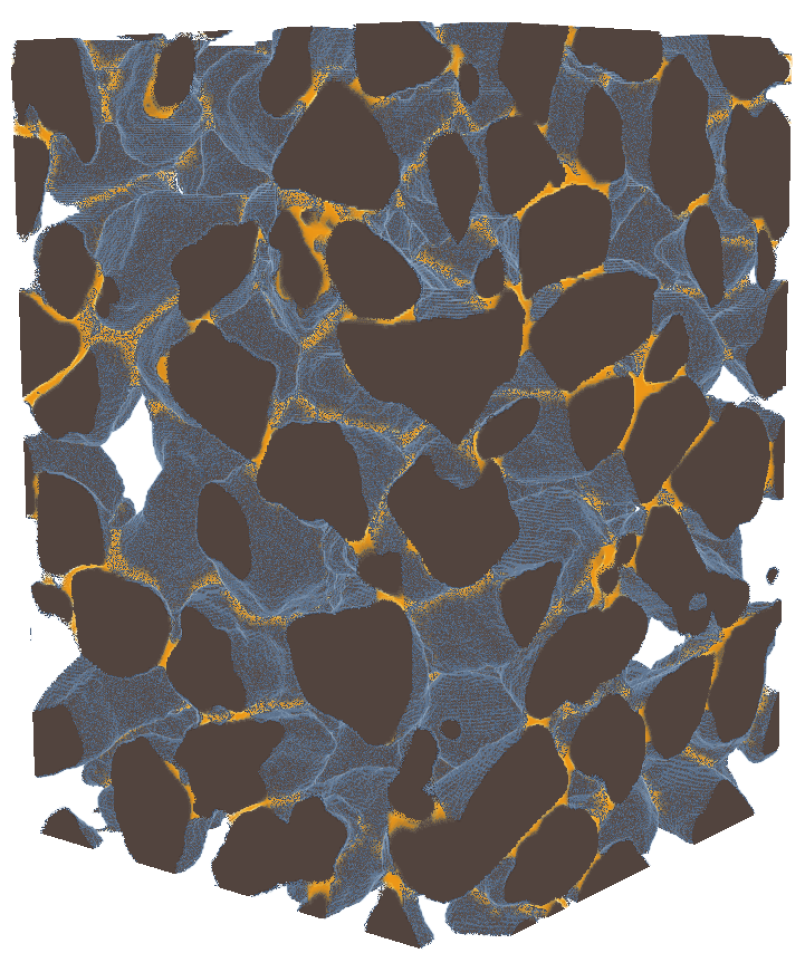
Generated microstructure of the 3D printed sand core material (black: sand grains - orange: binder).
Lukas Jabs, Matti Schneider Computational homogenization of particle-filled hollow sphere structures
To increase the machining speed and thus the productivity of machine tools while maintaining precision, it is necessary to effectively dampen the increased induced vibrations. In addition to the use of active methods, the use of passive methods, i.e., damping materials, is recommended. Sandwich materials with a core of particle filled hollow spheres (PHSS) represent a promising class of composite materials because they are lightweight, structurally integrated and offer passive, locally adaptive high damping. To specify the local composition of the PHSS and subsequently the local damping during the design of components, it is necessary to predict the material behavior based on the local microstructure. To achieve this prediction, we aim to develop new modeling approaches for PHSS using and extending available FFT-based homogenization methods.