General research topics
Computational micromechanics with the Fast Fourier Transform (FFT)
The goal of micromechanics is to deduce the mechanical behavior of a microstructured material, e.g., a fiber-reinforced composite, from knowledge of
- the microstructure, i.e., the spatial arrangement of the materials making up the microstructured material, the "phases",
- the constitutive behavior of the individual phases.
Such a procedure is convenient for reducing the experimental effort required to characterize anisotropic materials. Analytical estimates and bounds often make strong assumptions either on the microstructure or on the phase behavior to be able to derive the effective mechanical properties explicitly. In contrast, computational micromechanics uses simulations on real(istic) microstructures and relies upon rather complex material models for the phases.
To ensure compatibility with digital images of microstructured materials, e.g., micro-computed tomographcy (µ-CT), regular meshes based on so-called voxels (volume pixels) are used. However, traditional voxel-based finite-element approaches run into problems because of the large number of voxels, typically hundreds of millions or more, required to resolve microstructures of materials used in industry.
In the 1990s, Moulinec and Suquet introduced a novel computational approach to resolve micromechanics problems on regular grids based on the Fast Fourier Transform (FFT). In its initial state, the method was already able to handle inelastic constitutive laws and outperformed traditional voxel FEM significantly.
Since the beginning 2010s, we contributed to the understanding and progression of FFT-based computational micromechanics. Highlights include:
- Introduction of faster and more robust solvers, in particular for inelastic constitutive laws, leading to significant speed-ups.
- Development of alternative discretization schemes, including finite differences, finite elements and finite volumes. In particular, these ideas enabled to overcome the lack of convergence for porous microstructeres of the original method.
- Establishing the composite-voxel method which furnishes voxels with more than one phase with a dedicated constitutive law based on laminates. Composite voxels are indispensible for industrial-scale applications.
- Working out a sharp convergence theory for discretizations on a regular grid used in FFT-based methods. In particular, understanding the inherent superconvergence phenomenon of the effective stresses in micromechanics explains the unreasonable effectiveness of FFT-based computational micromechanics.
- Introducing more general boundary conditions in FFT-based computational micromechanics, both in terms of prescribed multi-axial stress- and strain states as well as more general conditions on the displacement fluctuation or normal stress on the boundary of the cell.
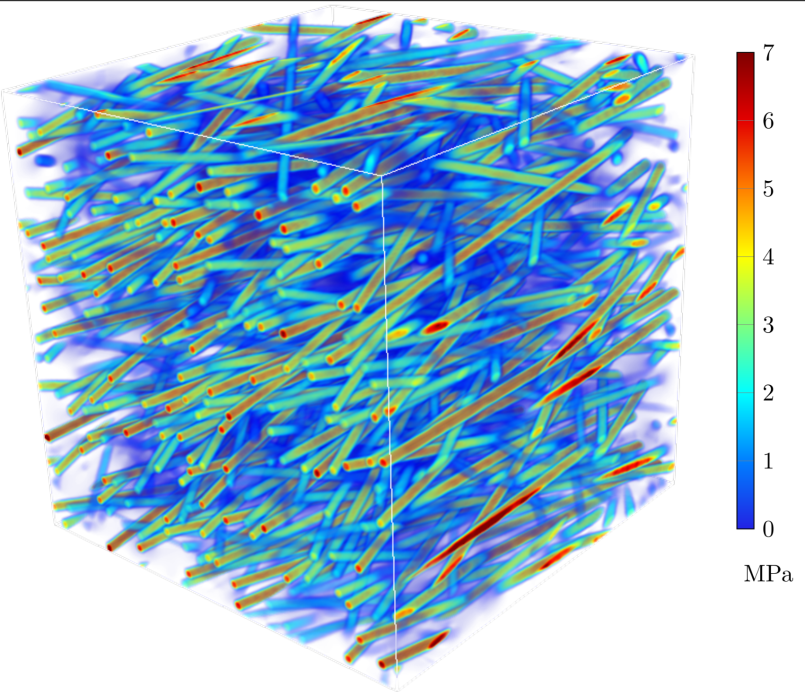
Local von-Mises stress in a fiber-reinforced composite.
Microstructure modeling
Microstructures serve as the "construction plan" for micromechanics. Hence, any mistake made in this "plan" has immediate consequences for the emerging effective properties of the material. Digital images of microstructures need to be supplemented by microstructure models for the same reasons as traditional mechanical experiments require constitutive models in the background: to dispense with "noise" and to provide a reasonable prediction for unseen data. Research of members of the institute concerns microstructure models for different material classes with random microstructure, and is typically based on geometric methods and optimization approaches. Fiber-reinforced composites: Short- and long-fiber industrial volume fractions, also sheet-molding compounds. Novelties include the Sequential Addition and Migration (SAM) algorithm, the efficient treatment of length distributions and several fiber orientation closure approximations.
- Granular materials: Modeling of sand-core microstructures based on a cluster-of-overlapping-spheres description of real sand grains and mechanical contraction, both for core blowing and additive manufacturing.
- Polycrystalline materials: Efficient generation of grain-based microstructures via Laguerre tessellations and semi-discrete optimal transport. High-accuracy texture-prescription via texture coefficients.
- Bicontinuous composites: Accurate schemes for such materials with prescribed anisotropy.
- Foams: Fast methods for computing dry and wet foams, also for intermediate states, e.g., for polyurethane foams.
We focus on creating periodic unit cells which are as small as possible while still maintaining a high fidelity representation of the statistics of the medium at large. As a consequence, the effort for the micromechanical computations get minimized.
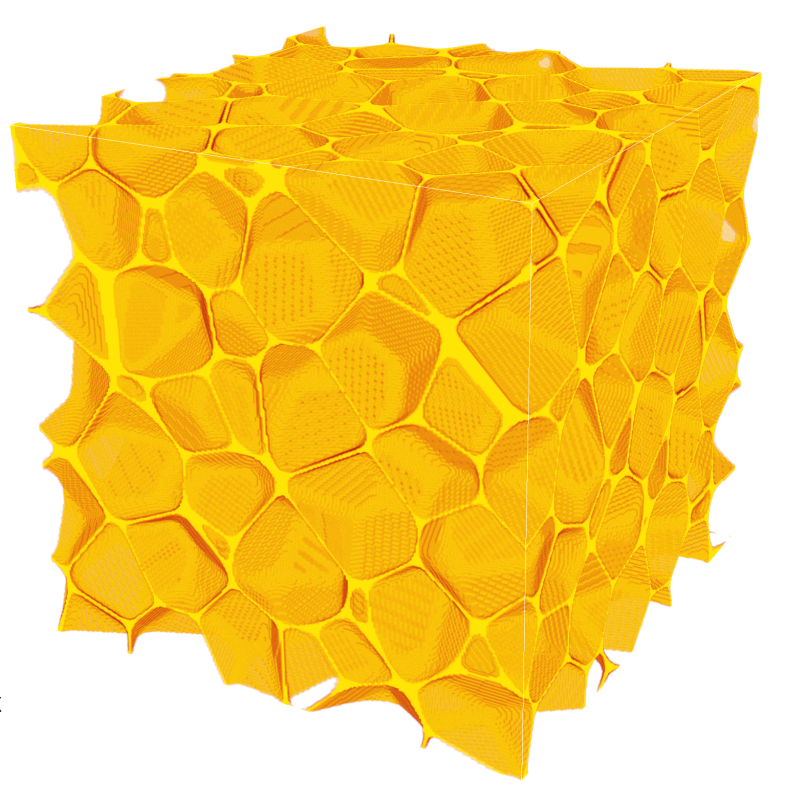
Generated closed-cell foam.
Upscaling in solid mechanics
As micromechanics serves to replace parts of the experiments, a natural focus lies on particularly costly experiments: those which are inelastic and take a long time to conduct. To feed associated FEM simulations of the component/specimen, dedicated material models for the microstructured material are required. Computational limitations preclude using numerical simulations of fully resolved microstructures within material routines directly. Rather, accurate surrogate models are imperative. There are different strategies to create such models, each balancing speed and accuracy in a specific way. Our contributions include:
- Model-order reduction strategies for estimating the fatigue behavior of fiber-reinforced plastic components. These strategies include dedicated material models for fatigue damage and a novel cycle-jump technique to make predictions in the high-cycle fatigue regime.
- Deep Material Networks (DMNs) provide a surrogate microstructure model based on hierarchical laminates and were introduced by Z. Liu and co-workers. We worked out the mechanics of the DMNs and introduced innovative computational strategies to achieve a speed-up of DMNs by a factor of 10⁶ compared to full-field simulations. Recent contributions include inverse parameter calibration of the phases, inelastic training strategies and applications to the viscosity of fiber suspensions.
- In case of a varying microstructure on component scale, e.g., changing fiber orientation, we worked out a general interpolation scheme which permits to mix arbitrary material models with possibly different internal variables. The simple and elegant idea became the industrial standard and found its way into commercial FEM software packages.